Responsibility
As one of the leading companies in our industry, Imperial Ductwork Services Ltd recognises that we have a responsibility not just to our clients, but also to our staff, the public at large, and the planet.
Ensuring Compliance and Sustainability on the Path to Net-Zero
As such, we acknowledge our industry’s various legal and ethical demands, and take every necessary and reasonable step to adhere to them.
This includes maintaining exceptional levels of Health & Safety compliance on every project we undertake, as well as implementing new and revolutionary methods to reduce our carbon footprint.
But we are not alone in our mission to lessen our environmental impact. Through partnerships with PlanetMark and other organisations, we are well on our way towards achieving our goal of net-zero carbon emissions.
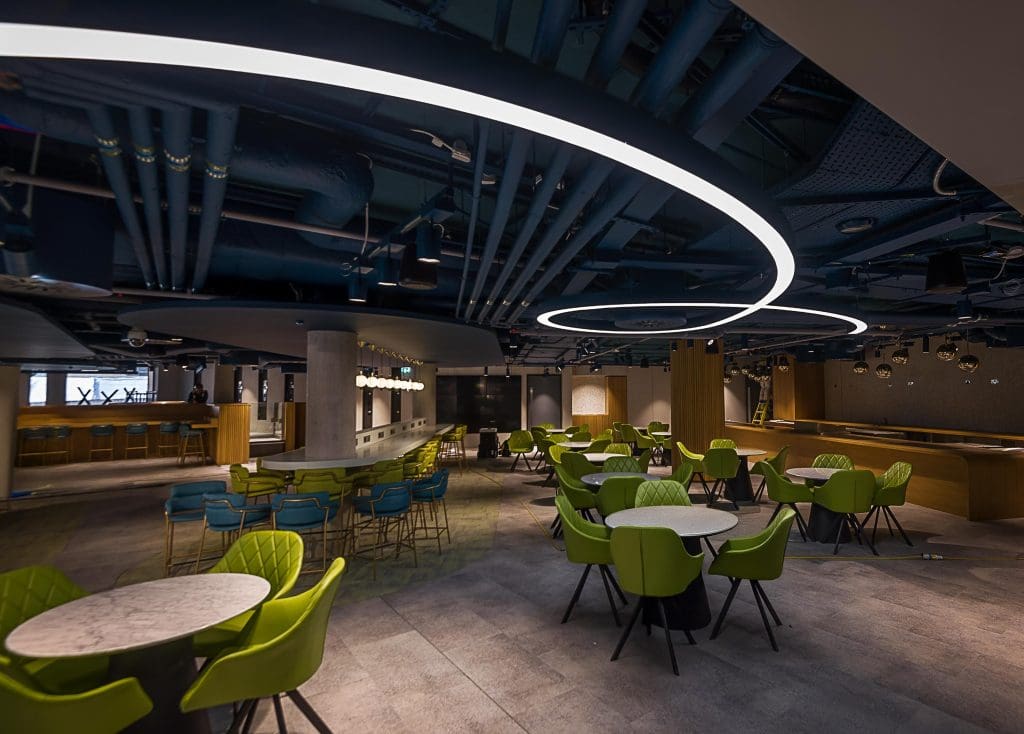
Partnership
Thanks to practices such as mining, concrete and steel production, and even transporting materials, the construction industry is responsible for around 40% of global carbon emissions. This number increases exponentially when you consider the energy required to power, heat and cool virtually every building on the planet.
As specialists in ductwork and ventilation systems, we understand that our business directly contributes to this alarming statistic. However, we also appreciate that this puts us in a unique position to do something about it.
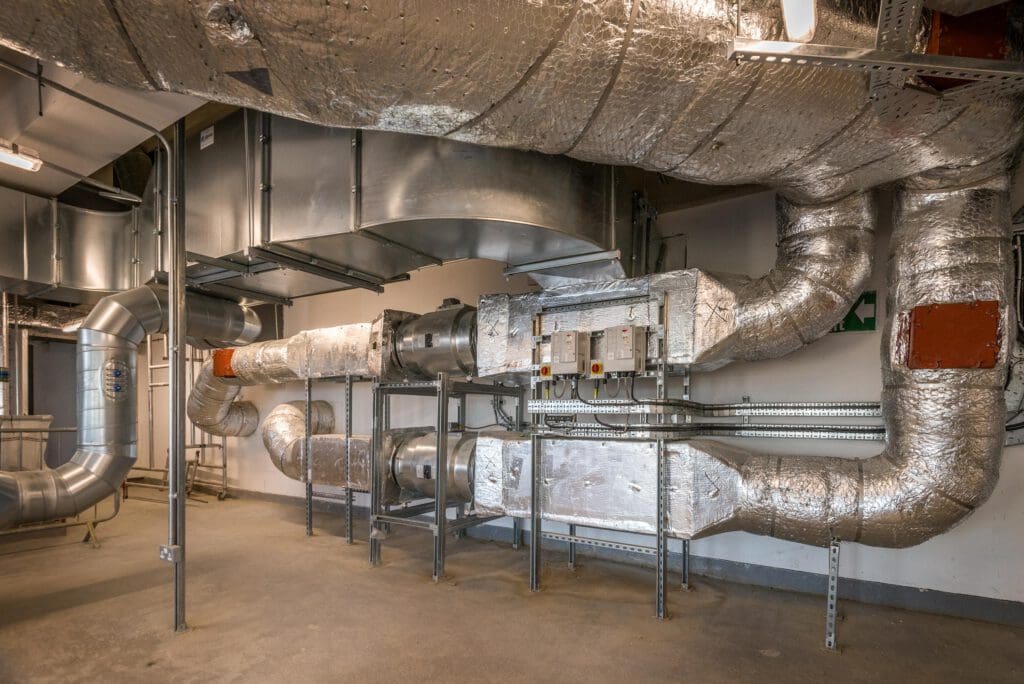
IDSL’s Commitment to Reducing Emissions and Industry Leadership
IDSL is an active member of the Supply Chain Sustainability School, which is dedicated to integrating and advancing sustainability practices throughout the built environment industry. As a member, we gain direct access to regular CPD training, as well as ongoing, tailored support to achieve our sustainability goals.
Furthermore, we have been awarded PlanetMark certification for reducing our measured Scope 1 and Scope 2 emissions (market-based) by 59.3% absolute reduction and a reduction of 64.5% per employee (market-based) compared to our previous year of trading. This marks the second consecutive year that IDSL has achieved PlanetMark Business Certification.
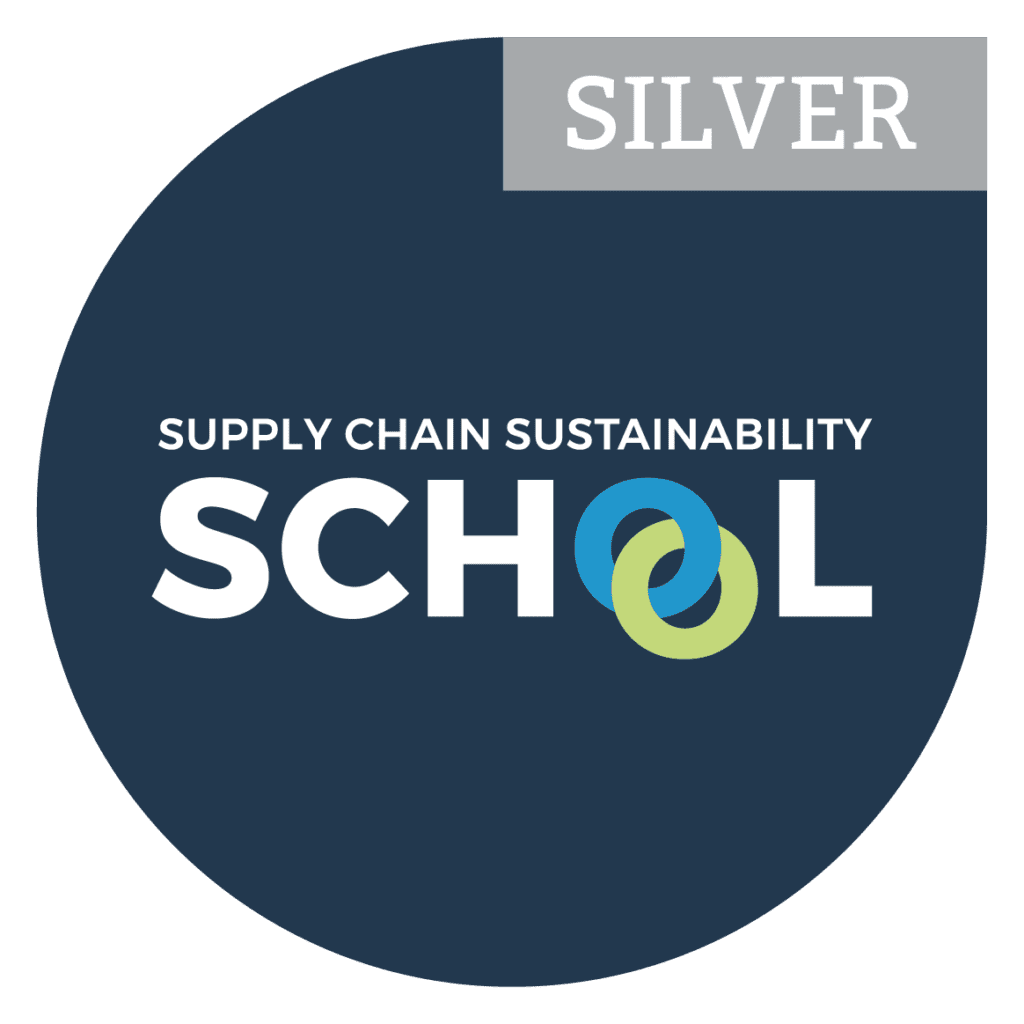
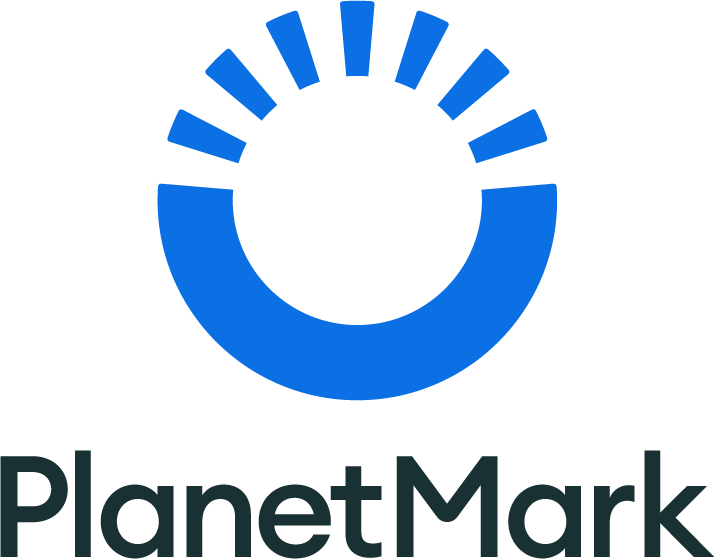
Some of the ways we have achieved this include:
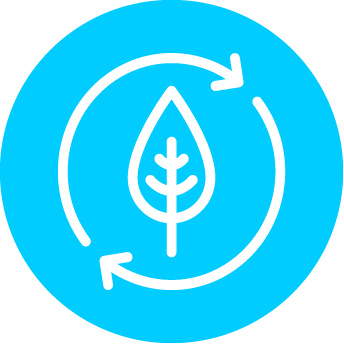
Procuring and fabricating sustainable materials
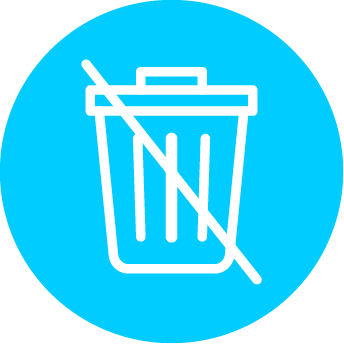
Responsible and compliant waste management
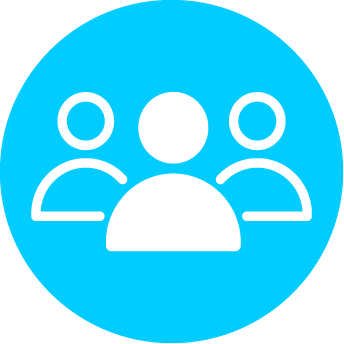
Staff engagement in environmental impact training programmes
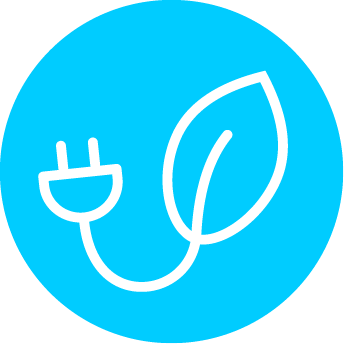
Reducing energy and fuel consumption across the business
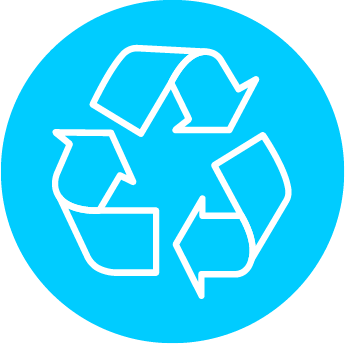
Promoting recycling and waste reduction
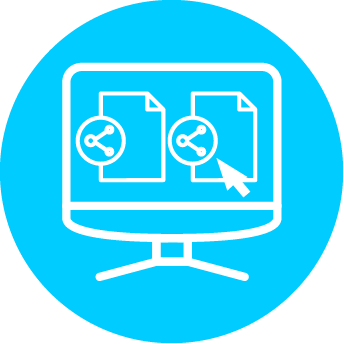
Investing in cutting-edge software and technologies to improve efficiency and reduce waste
Steps Towards Achieving Net-Zero Carbon Emissions
We are proud to have also formed a strategic partnership with ArcelorMittal on our joint journey to Net Zero, and are targeting the procurement of over 1000 tonnes of lower embedded carbon (LEC) steel by the end of 2025.
This reflects real life-cycle savings of 1,694 tonnes of Co2e.
We recognise there is still plenty more to do before we reach our net-zero carbon emissions goal. That is why IDSL is currently considering the following steps to reduce our Scope 3 emissions:
- Working with suppliers and companies who are also engaged in reducing their carbon footprint
- Implementing regular energy and waste management audits throughout the company
- Introducing water usage awareness campaigns in communal kitchen areas and WC facilities
- Arranging safe and fuel-efficient driving training for all our drivers
- Installing smart meters across the company
- Investing in more fuel-efficient vehicles and introducing fuel cards
- Buying paper from sustainable forests or made from recycled content
Green Steel
As one of the most highly versatile and commonly used materials in the world, more than two million tonnes of steel is manufactured every year. Steel is not only used for making everyday items such as cookware, tools, appliances and transportation vehicles, but for decades it has been an essential component of the construction industry. Whether in the form of girders and beams to hold up structures like bridges and buildings, or simply in the screws, nuts, bolts and tools necessary to build them, steel production is always in high demand.
However, with the steel industry alone responsible for roughly 8% of global CO2 emissions, it is essential that companies like ours find and implement ways to make it more green.
To this end, IDSL is proud to manufacture decarbonised, green steel at our very own manufacturing facilities in Dartford, Kent.
While traditional manufacturing processes involve the use of blast furnaces burning fossil fuels to reach the required temperatures, green steel furnaces rely on renewable energy sources such as solar, wind and hydropower for fuel. But this is just the beginning.
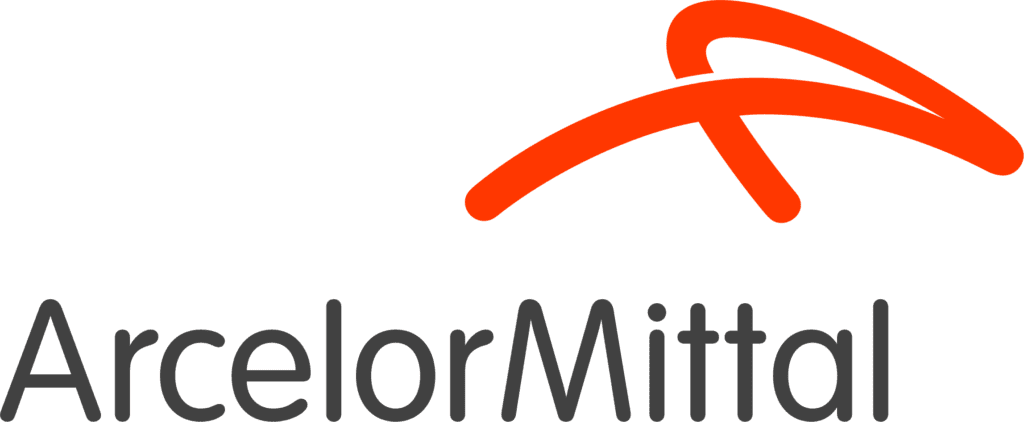
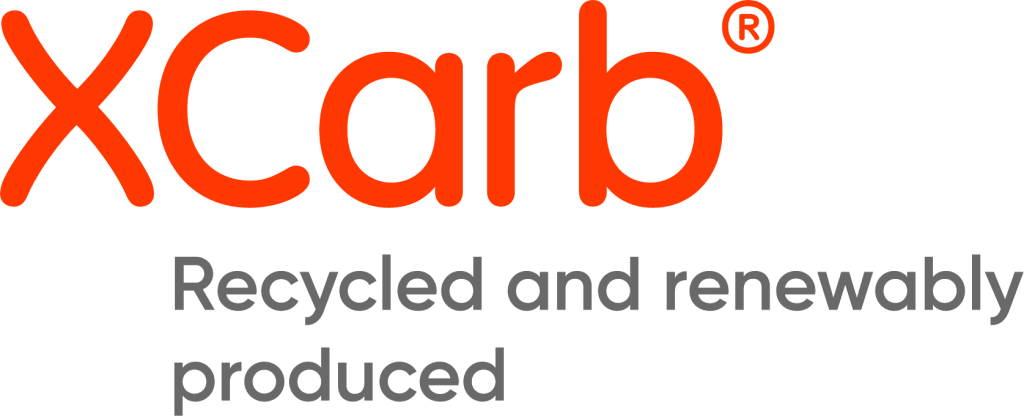
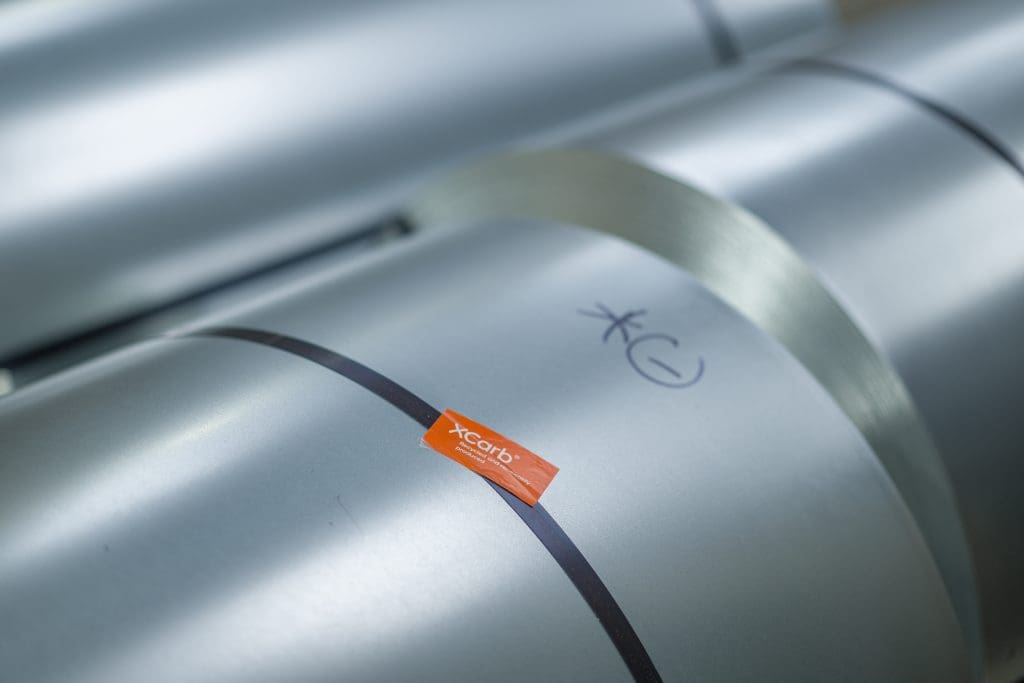
The Production Process
1
Direct Reduced Iron (DRI)
Traditional steel is made by combining iron ore and carbon at high temperatures, resulting in iron and carbon dioxide. However, by combining iron ore with hydrogen, only iron and water (in the form of steam) are produced.
2
Scrap Steel Recycling
Instead of adding primary elements such as nickel, chromium and manganese to create an alloy, recycled steel is mixed with this liquid iron. Not only does this reduce waste and improve efficiency, but it also eliminates the need to mine for further primary elements.
3
Carbon Dioxide Capture
Carbon-capture technology is used to capture CO2 emissions generated during the steelmaking process and stores them underground, preventing carbon dioxide from ever entering the atmosphere. This significantly contributes to a more environmentally friendly process of steel production.
4
Processing Iron
The reduced iron is then processed into liquid hot metal using an electric furnace operating on renewable energy sources.
5
Minimising Waste
Recycling the by-products of steel production keeps waste to a minimum; as does utilising efficient methods of production such as using ammonia as a reducing agent, electrolysis to split water into oxygen and hydrogen, and digitalisation for optimal efficiency.
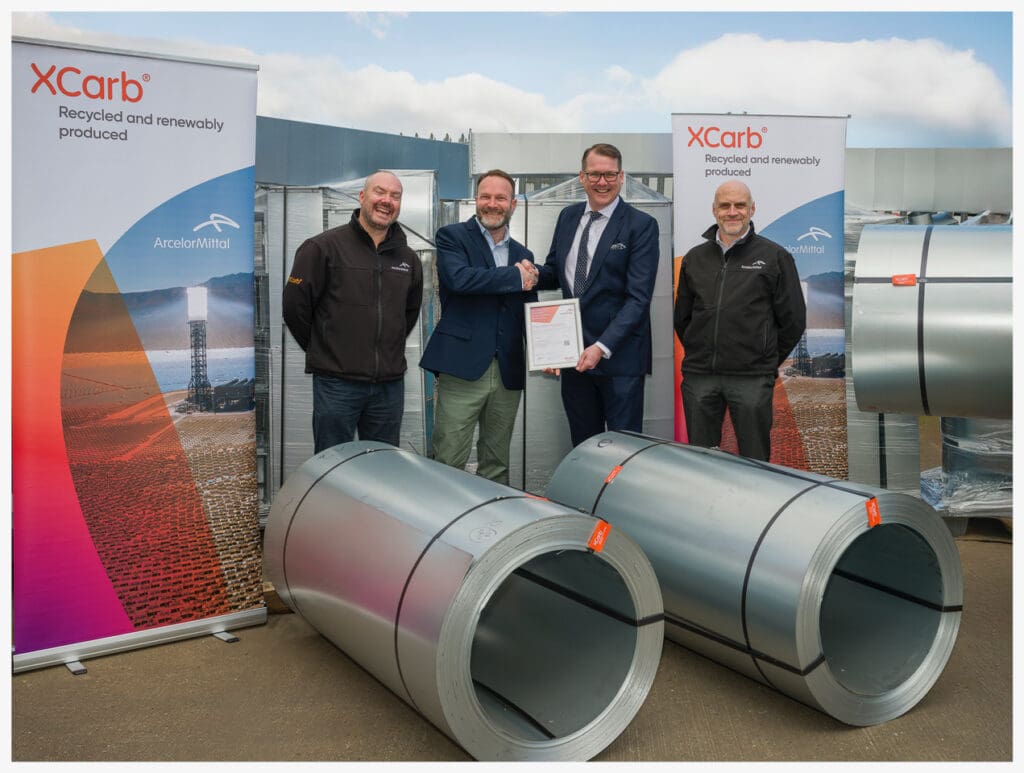
Our Commitment to Sustainable Steel: Net-Zero Manufacturing with XCarb®
As part of our commitment to achieving our net-zero goal, we pledge to manufacture all our ductwork production out of our Dartford factory using XCarb® recycled and renewably produced steel. XCarb® RRP steel reduces
Co2 emissions by 65% compared to traditional steelmaking, supporting IDSL’s commitment to decarbonisation and carbon footprint reduction.
In addition, IDSL and ArcelorMittal will supply LEC steel ductwork to live and future projects across the UK, ensuring that sustainability remains at the heart of our core values.
Get In Touch
Whether you require full turnkey installations or supply-and-install packages, contact our expert team today for high-quality, tailored ductwork solutions to suit your needs.
MANUFACTURING